As an experienced medical cable manufacturer, we recognize the significance of meticulously choosing conductor, insulation, and jacket materials throughout the cable manufacturing process. Material selection plays a pivotal role in defining a cable’s performance, safety, and compatibility with various sterilization methods. Leveraging our expertise in material selection, we provide tailored solutions that precisely align with our clients’ needs, ensuring superior quality and reliability in every cable we produce.
As a crucial component of healthcare interconnect solutions, medical cable manufacturing plays a vital role in the healthcare industry. Designing medical cables requires careful consideration, including the selection of conductor materials, wire gauges, the necessity of shielding, materials’ high-temperature resistance, sterilization methods, choice of cable outer diameter (OD), and whether the cable is intended for single-use or reusable purposes.
Therefore, we must select appropriate materials that meet the product’s performance, usage, environmental, and aesthetic requirements.
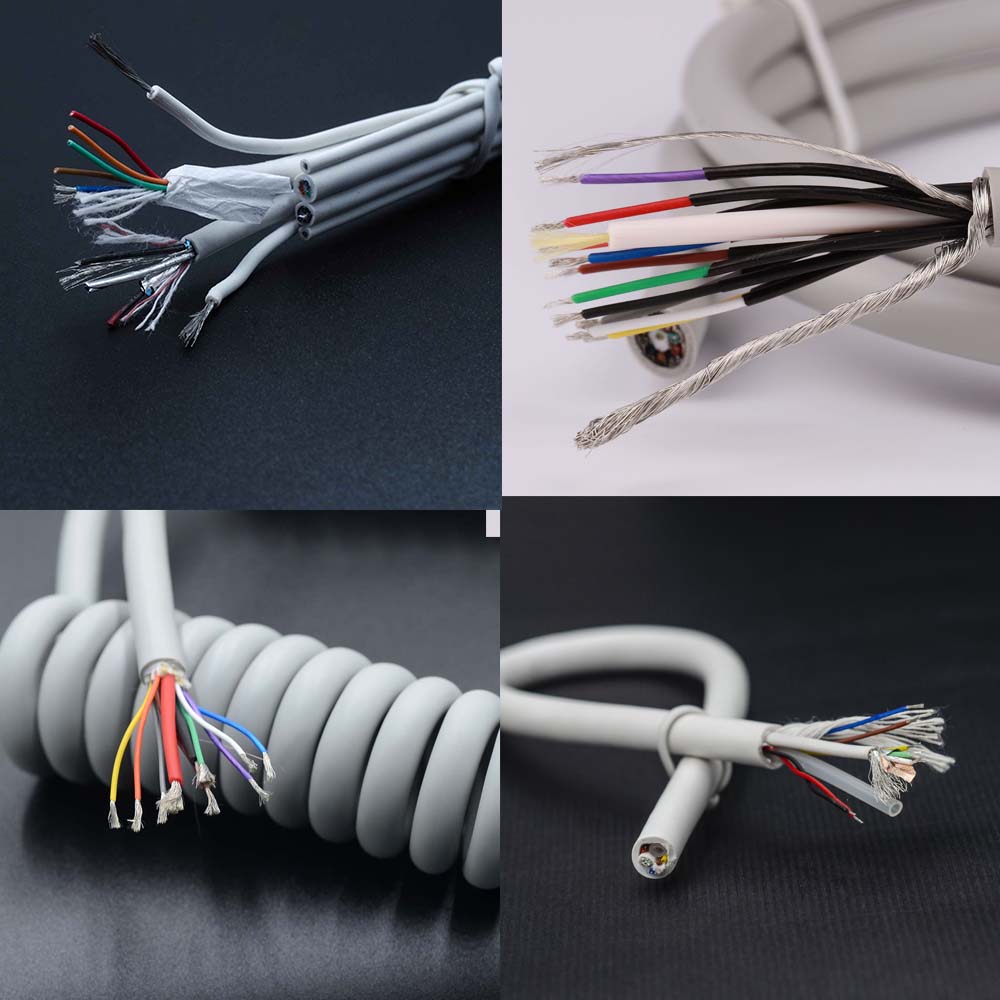
What factors should be considered when determining the cable structure?
The structure of medical wires is typically determined based on their application requirements in the medical field and the desired performance characteristics.
In terms of purpose and application scenarios, different medical fields and applications may require different types of wire structures. For example, pacemakers require wires that are corrosion-resistant, flexible, and highly conductive, while endoscopes may require finer and more bendable wires.
In terms of biocompatibility, medical wires need to have excellent biocompatibility to avoid irritation or adverse reactions in human tissues. Material selection and surface treatments of the wires can affect their biocompatibility.
In terms of size and diameter, some medical applications require very fine wires for use in minimally invasive surgery or endoscopic procedures. In these cases, the diameter of the wires needs to be considered.
In terms of cost and manufacturability, the structure of the wires is also influenced by manufacturing costs and manufacturability. Complex structures may increase manufacturing costs or manufacturing difficulties.
Additionally, various performance factors such as sterilization requirements, conductivity, noise isolation capabilities, flexibility, bending resistance, and tensile strength index need to be considered. YQF cable have designed thousands of cables,ranging from simple to highly complex to meet different sterilization methods and other requirements, such as high-flex cables and low triboelectric noise. In designing medical wires, YQF cable begins with reviewing our customer’s requirements. This process involves selecting the right materials that meet the product’s performance, usage, environmental, and aesthetic needs.
Successful custom medical cable manufacturing requires the correct cable design, tool design, material choice, and processing methods. We has designed thousands of cables, overmolds, and assemblies ranging from the most simplistic to very complex to meet different sterrilization method and other requirement,such as High flex cable,Super low triboelectric noise…
Jacket material mainly related with the sterrilization and conductor material matters a lot on flexbility and electronic properties.
The Application Environment For Medical Cables
Medical cables are usually potential to touch skin and need to sterillize .during the design and manufacturing,following issues is worthy of our attention:
• Disposable/Reusable cable designs
• Low noise shielding
• Resistance to steam, gamma, ETO and other sterilization methods
• High temperature insulators
• Hi-Flex and long-life cable designs
• Potting and pressure testing
• Chemical Resistance
• Serialization and lot control
• Statistical process control
• Medical-grade materials – including TPE, polyurethane and silicone
• EMI suppression
Suitable Sterrilization Methods List Based On Different Materials
Download-Different Sterrilization method for different Jacket material of wire&Cable.pdf
Material reference
Conductor Options | Shielding Options | Enhancement Options | Insulation & Jacketing Materials | |
Bare Copper | Bare Copper Braid | Strength Members | CPE/Chlorinated Polyethylene | PFA/Perfluoroalkoxy |
Tinned Copper | Tinned Copper Braid | Water Blocking | EPDM/Ethylene Propylene Diene Monomer | PFE/Perfluoroelastomer |
Silver Plated Copper | Silver Plated Copper Braid | Fillers | ETFE/Ethylene Tetrafluroroethylene | PP/Polypropylene |
Nickel Plated Copper | Nickel Plated Copper Braid | Rods | FEP/Fluorinated Ethylene | PTFE/Polytetrafluoroethylene |
High Strength Alloys | High Strength Alloys Braid | Tubes | Foamed FEP | PUR/Polyurethane |
Copper Clad Steel | Copper Clad Steel Braid | Foamed PFA | PVC/Polyvinyl Chloride | |
Prebonded Conductor | Stainless Steel Braid | Foamed PE | Silicone | |
Overcoated Conductor | Aluminum Mylar Foil Shield | Foamed TPE | Tefzel | |
Topcoated Conductor | Spiral Shield | Halar | TFE/Tetrafluoroethylene | |
HDPE & LDPE | TPE/Thermoplastic Elastomer | |||
Hytrel | TPR/Thermoplastic Rubber | |||
mPPE/Modified Polyphenylene | XLPE/Cross-Linked Polyethylene | |||
Neoprene | XLPO/Cross-Linked Polyolefin | |||
PE/Polyethylene |
Conductor Accommodation
In medical cable assemblies, conductors are typically materials used to transmit electrical signals or power. Based on the mechanical and electrical performance requirements of medical cable assemblies, the following conductor options are available:
1. Bare Copper: Bare copper conductor refers to copper wire without any coating or insulation treatment.
2. Tin-plated Copper: Tin-plated copper conductor involves coating the surface of copper wire with a layer of tin to improve its corrosion resistance.
3. Silver-plated Copper: Silver-plated conductor involves adding a silver coating to copper wire to enhance its conductivity and corrosion resistance.
4. Nickel-plated Copper: Nickel-plated conductor involves electroplating or chemically depositing a layer of nickel onto the surface of copper material.
5. Alloy: Alloy conductor is made of a combination of different metals, usually aiming to balance electrical conductivity, mechanical strength, and other properties.
6. Copper-Clad Steel: Copper-clad steel conductor is a composite conductor with copper coating around steel wire.
7. Coated Conductor: Coated conductor involves applying a layer of non-metallic material or alloy material on the surface of the metal conductor.
8. Carbon Fiber Conductor: Carbon fiber is a fiber material composed of carbon atoms, characterized by lightweight, high strength, and corrosion resistance.
9. Tinsel (Foil lined aramid fiber): Tinsel conductor typically consists of one or more fine strands of aramid fiber surrounded by thin foil, usually silver foil or tin foil.
……and so on
We have the ability to produce 44AWG-14AWG wire gauges,we have developed proprietary wire constructions that offer signal and mechanical performance advantages for medical device patient lead-wire applications that demand low triboelectric noise.
姓名 | Advantages | Disadvantages |
Bare Copper | Copper has good conductivity and relatively low cost. | Copper is prone to oxidation and corrosion, especially in specific environments like high humidity or strong chemical corrosion. |
Tin-plated Copper | Tin plating on copper conductor enhances corrosion resistance and oxidation resistance, aiding in conductor protection. | Tin plating may melt in some high-temperature environments, leading to performance degradation. |
Nickel-plated Copper | Nickel-plated copper conductor retains the high electrical conductivity of copper while enhancing resistance to corrosion and oxidation, making it more robust and aesthetically pleasing. | Nickel plating may increase difficulty in soldering and has lower environmental friendliness. |
Silver-plated Copper | Offers higher conductivity than copper. It can provide better signal transmission and corrosion resistance. | Silver is more costly and prone to tarnishing. |
Copper Alloys and Other Conductive Alloys | Some alloy conductors, such as copper-nickel alloys, can balance conductivity and mechanical strength. | Sacrifices some conductivity depending on alloy composition. May require special processing, increasing manufacturing costs and complexity. |
Copper-Clad Steel | Offers higher mechanical strength, suitable for applications requiring tensile and bending resistance. | Relatively lower conductivity, relatively difficult soldering, and heavier weight. |
Coated Conductors | High conductivity, high thermal conductivity, corrosion resistance, and does not significantly increase the weight or change the flexibility of the conductor. | Higher cost, challenges remain in preparation technology and reliability. |
Tinsel (Silver Foil, Tin Foil) | Flexible, can pass 1 million bend tests. Tinsel lead wire with Silver conductor has good conductivity and relative low resistance, Tinned Copper wire conductor Tinsel is a relatively economic solution | Lower strength, prone to damage from stretching. |
Carbon Fiber | Lightweight characteristics; does not produce significant imaging effects in X-ray, gamma-ray, and other electromagnetic wave bands. | Slightly higher cost, difficult to process. |

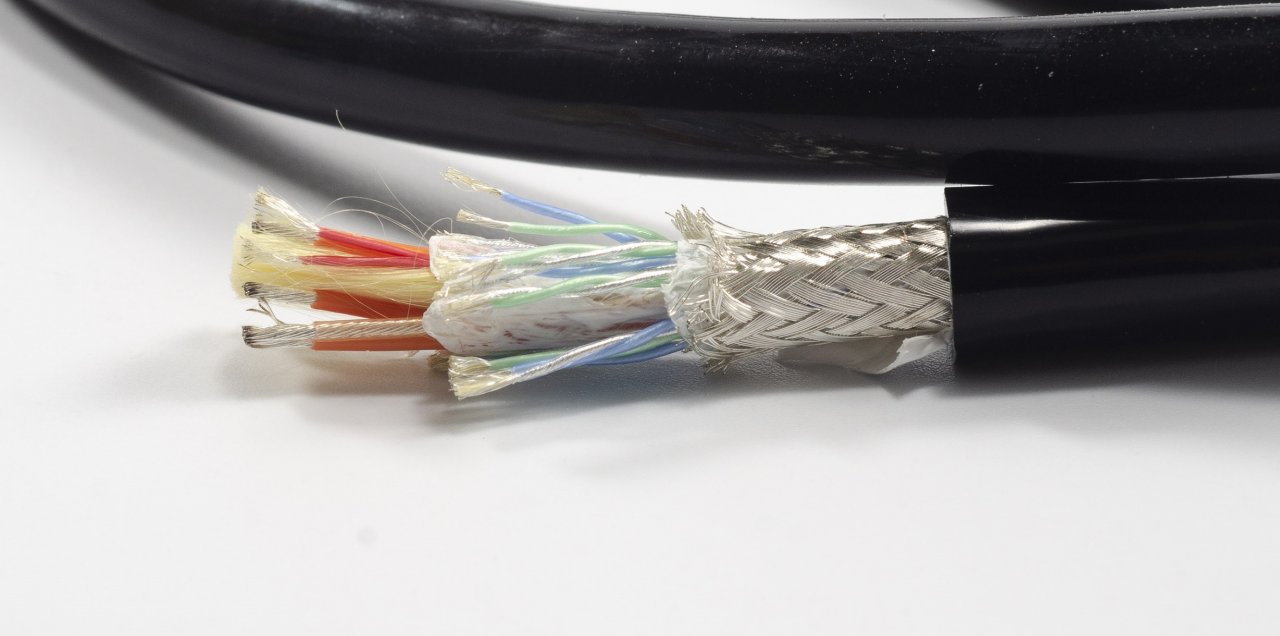
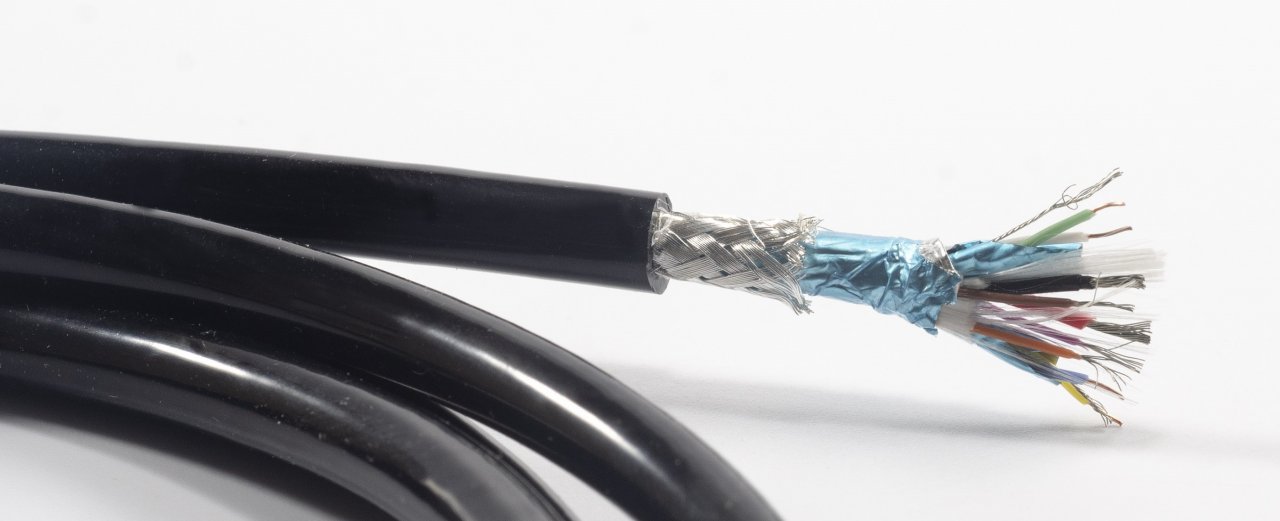
Shielding
Shielding is essential to protect the internal signals of the cable from external electromagnetic interference, ensuring the reliability and accuracy of medical devices. EMI and RF interference can degrade signals, making diagnosis difficult or even impossible for your medical cable assembly application. Effective shielding can reduce unwanted interference and minimize the need for active filtering within your medical device.
YQF Cable can offer expertise in braided, spiral serve, foil, and foil combination shielding, assisting your team in selecting the most suitable option for your application while ensuring that shields can be properly terminated and remain effective. You can choose from various shielding materials, such as:
- Bare copper braided layer/spiral layer
- Tin-plated copper braided layer/spiral layer
- Silver-plated copper braided layer/spiral layer
- Nickel-plated copper braided layer/spiral layer
- Copper-clad steel braided layer/spiral layer
- Aluminum foil shielding
- And more…
Jacket Materials
We take into consideration appropriate and reliable medical grade, bio-compatible materials for use in cable jacket materials for your medical cable assembly. Considerations such as appearance, flexibility and feel, application environment, material biocompatibility,protection of conductors, durability, cleaning, disinfection and sterilization are taken into account when assisting our customers to select the right cable jacket material. Common jacket materials include:
·Thermoplastic Elastomer –TPE (Santoprene, Versaflex)
·Thermoplastic Urethanes –TPU
·Silicone
·PVC
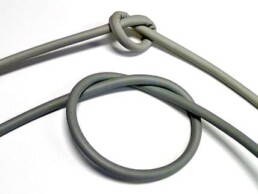
姓名 | Advantages | Disadvantages |
Polyurethane (TPU) | – Good flexibility and strong abrasion resistance, suitable for bending applications. – Good biocompatibility and easy processing. | – May be sensitive to certain chemicals in some cases and not suitable for high-temperature or high-pressure environments. |
Thermoplastic Elastomer (TPE) | – Good flexibility and excellent bending performance. – Excellent biocompatibility and processability. | – Some types of TPE may be sensitive to certain chemicals and not suitable for high-temperature applications. |
Silicone | – Excellent biocompatibility, high and low-temperature resistance, and flexibility. | – Relatively high cost. – Some types of silicone may be brittle and not suitable for high-strength applications. |
Polyvinyl Chloride (PVC) | – Low cost. Suitable for many disposable medical devices. | – Some types of PVC may contain phthalates and other suspected harmful substances, so special treatment may be required to ensure biocompatibility. |
Other issues to consider
As an experienced medical cable factory, we usually ask you the following questions when communicating with you, which are also some issues that you need to consider when selecting cables;